Thanks: Leire Asensio-Villoria, Kathy King, Kyla Toomey, Mitch Shiles, Kevin Hinz, Jake Rudin
Team: Tanuja Mishra, Zhiwei Liao, Andrew Kim, Sizhi Qin
Year: 2016
Site: Gallery 224, Office of the Arts, Harvard Univeristy
Team: Tanuja Mishra, Zhiwei Liao, Andrew Kim, Sizhi Qin
Year: 2016
Site: Gallery 224, Office of the Arts, Harvard Univeristy
RAse
The intention of the project was to explore the possibilities of architectural form finding through an innovative fabrication technique, which is a combination of the robotic arm and the turntable. The hand-manipulated processes of the potter’s wheel were abstracted into simpler movements, which could then be translated into the robotic manufacturing process. The robotic technology combined with digital scripting tools was then used to expand the form-generation capabilities of the pottery-making process. This merging of techniques not only introduced novelty in terms of forms but also made the structures more amenable to mass production. Mechanization of these manufacturing processes has allowed for speeding up the pace and the scale of manufacturing.
The stages of manufacturing entailed a combination of analog and digital methods - involving the processes of extrusion, rotation, robotic carving, firing and assembly. The pieces were shaped into slightly varying configurations of spiral forms. A mirrored aggregation method was developed to allow for lateral bracing of the individual columns with those that were adjacent to them. Some potential areas of application would be in designing expressive architectural screens, structures for evaporative cooling and porosity screens for privacy control or natural lighting control.




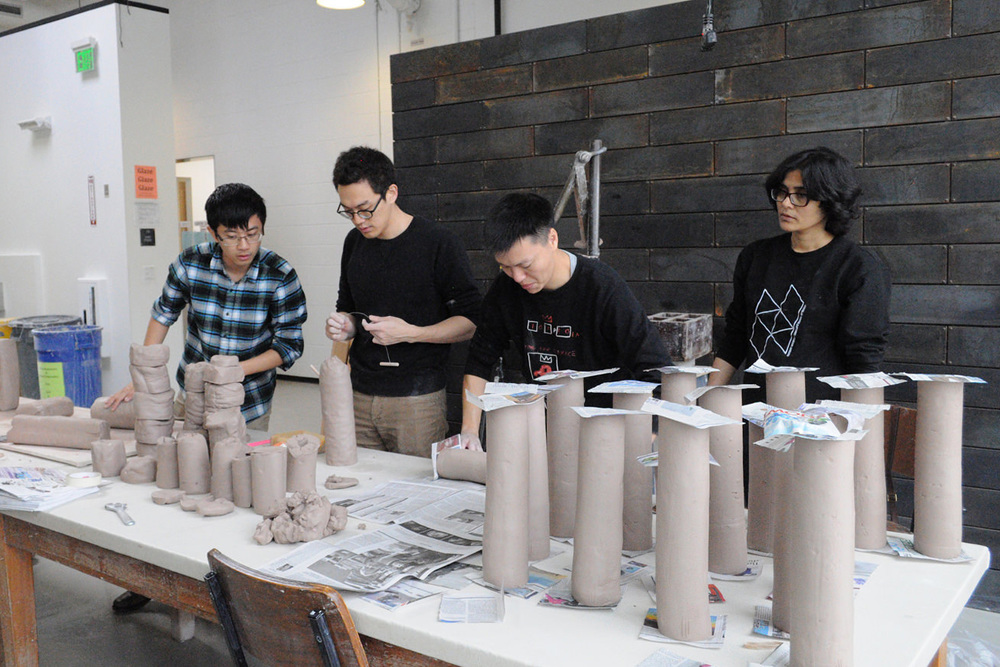

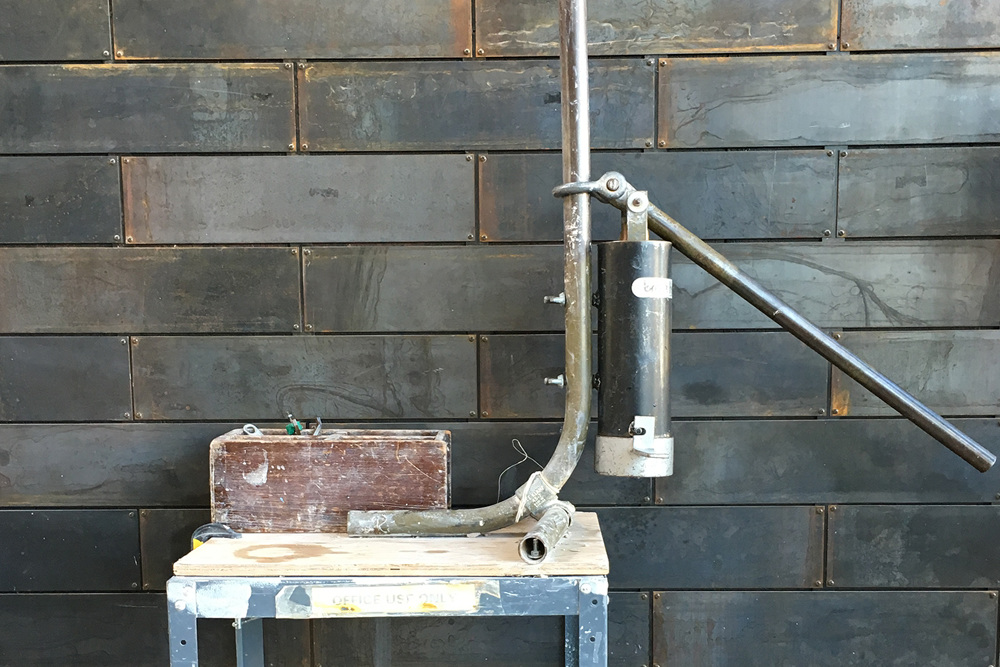
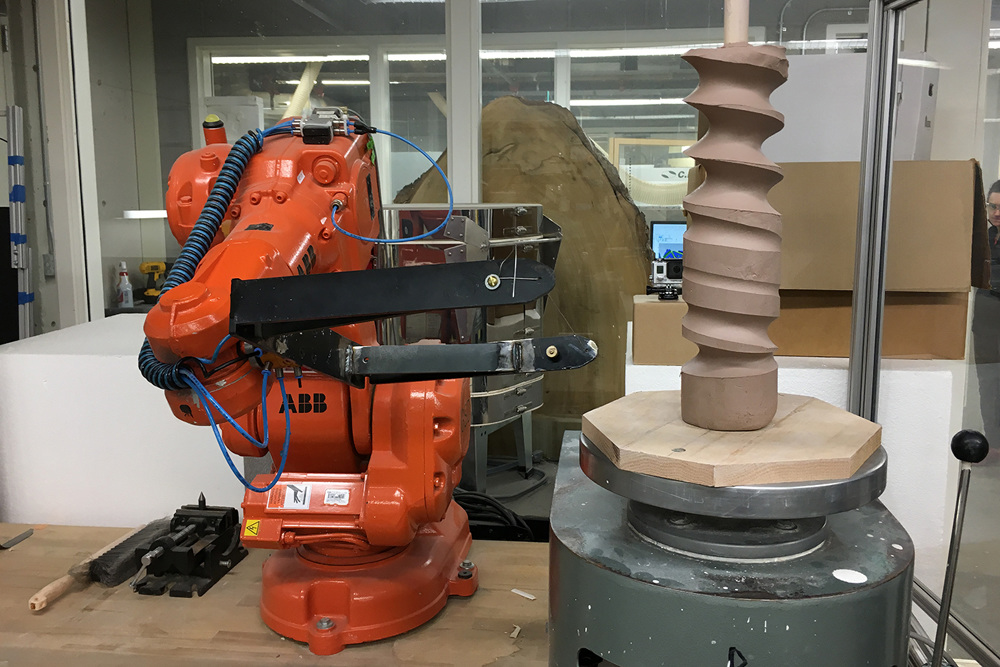

Copyright © 2021 Tanuja Mishra. All rights reserved.